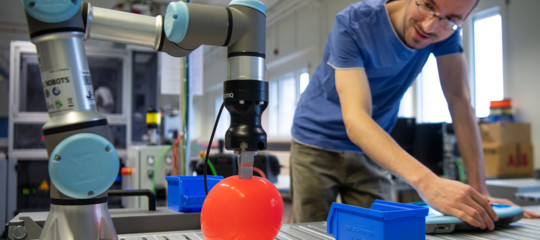
(Afp)
Industria 4.0
Rold di Cerro Maggiore e la Divisione Farmaceutica Bayer di Garbagnate (entrambe in provincia di Milano) sono le due fabbriche italiane scelte da McKinsey e World Economic Forum tra i 16 “impianti faro” dell’Industria 4.0 mondiale.
Le due fabbriche italiane
Rold è l’unica Pmi presente nell’elenco. Con 240 dipendenti produce meccanismi di chiusura per lavatrici e lavastoviglie. “Utilizza tecnologie di Industria 4.0, come smartwatch, prototipazione rapida e cruscotti digitali, che hanno contribuito a migliorare il fatturato tra il 7% e l’8%”. Bayer Divisione Farmaceutica “ha adottato soluzioni digitali e utilizzato i dati per migliorare significativamente la produttività”. In un momento di forte crescita dei volumi produttivi, ha utilizzato un “gemello digitale” (cioè un’immagine degli impianti frutto di sensori e dati) per migliorare il controllo qualità.
Il caso Rold
L’impianto Rold, oltre a essere l’unico italiano per proprietà e non solo per geografia, è stato uno dei due casi approfonditi dal rapporto assieme al sito Procter & Gamble di Rakona (Repubblica Ceca). “Rold – spiegano McKinsey e Wef – dimostra che la quarta rivoluzione industriale è possibile anche con investimento limitati”, grazie alla “collaborazione con fornitori e università”. “Le ragioni che ci hanno spinto a introdurre tecnologie digitali – ha spiegato il presidente di Rold Laura Rocchitelli – sono diverse: prima di tutto, la produzione sarebbe diventata più efficiente.
L’opportunità di monitorare in tempo reale i processi è essenziale per raggiungere risultati migliori”. Stefano Bosani, capo del reparto stampaggio, sottolinea come “la piattaforma digitale permette al supervisore e ai lavoratori di avere costantemente sott’occhio il processo”. E anche i lavoratori sottolineano i vantaggi derivanti da una produzione basata su “dati oggettivi piuttosto che su percezioni soggettive”.
Uno degli aspetti sui cui il rapporto torna spesso è proprio la componente umana dell’impianto milanese. “Rold – ha aggiunto Rocchitelli – immagina una fabbrica in cui le soluzioni digitali e l’automazione forniscano il miglior supporto possibile per gli operatori”. E per una Pmi, la trasformazione non sarebbe stata possibile senza il coinvolgimento di tutti: “Abbiamo dovuto creare consapevolezza tra i lavoratori sull’opportunità di utilizzare tecnologie digitali, con un approccio inclusivo”.
Come sono stati scelti i “fari”
“Molte aziende – afferma il rapporto per spiegare come sono stati selezionati i ‘fari’ dell’Industria 4.0 – stanno pilotando la quarta rivoluzione industriale nel settore manifatturiero, ma poche sono riuscite a integrare le tecnologie su vasta scala registrando significativi risultati economici e finanziari”. La selezione delle eccellenze è passata da un esame di oltre mille candidati e da una visita diretta in fabbrica. I vincitori rappresentano “l’avanguardia”. Sono “fari per il mondo perché rappresentano l’approccio alla produzione che può guidare la futura crescita economica globale.
Dimostrano come impegno e lungimirante possano creare un mondo migliore. Allo stesso modo – continua lo studio – illustrano come la rivoluzione possa trasformare la natura del lavoro, coinvolgendo i lavoratori e migliorando le loro competenze”. Osservando gli impianti migliori, McKinsey e Wef hanno individuato “tre grandi tendenze”: “Intelligence, connettività e automazione flessibile”. Lo studio sottolinea che i casi concreti di Industria 4.0 cancellino “miti e false credenze”: “I fari sono la prova dei benefici della rivoluzione digitale”, non solo in termini di efficienza ma anche di lavoro. Gli impianti leader sono “iniettori di capitale umano. Piuttosto che sostituire i lavoratori con le macchine, stanno trasformando il lavoro rendendolo meno ripetitivo, più interessante e diversificato”.
Quali sono gli altri impianti modello
Oltre a Rold e Bayer di Garbagnate, ecco quali sono le fabbriche scelte da McKinsey e Wef:
– Bmw (Regensburg, Germania) ha prodotto 320.000 veicoli nel 2018 usando la piattaforma IoT del marchio tedesco. Sono stati necessari importanti investimenti, ma adesso la fabbrica è più flessibile, tanto da tagliare dell’80% i tempi di adozione di nuove applicazioni.
– Bosch Automotive (Wuxi, Cina) sfrutta l’analisi dei dati per leggere, migliorare e simulare, con il risultato di prevedere il blocco delle macchine prima che avvenga.
– Danfoss (Tianjin, Cina) produce compressori per frigoriferi e impianti di condizionamento. Utilizzando il suo sistema di tracciabilità completamente digitale, ha migliorato la produttività del 30% e diminuito i reclami dei clienti del 57% in due anni.
– Fast Radius e UPS (Chicago, Usa) hanno applicato la stampa 3D su base industriale per creare una produzione più personalizzata. Anche in questo caso, l’analisi in tempo reale dei dati è la base per gestire design, produzione e consegne.
– Foxconn (Shenzhen, Cina) è la fabbrica dove si assemblano componenti per smartphone (a partire dagli iPhone) e altri dispositivi. Gli impianti sono autonomi non solo nel momento della produzione: apprendono dai processi per migliorarli e per gestire una sorta di auto-manutenzione. Risultato: efficienza aumentata del 30%.
– Haier (Qingdao, Cina) ha spostato sul web il processo di configurazione e vendita dei propri prodotti (condizionatori d’aria). I tempi di consegna sono stati tagliati di un terzo e la produttività è cresciuta del 64%.
– Johnson & Johnson DePuy Synthes (Cork, Irlanda) utilizza la Internet of Things per creare un “gemello digitale” degli impianti, cioè una rappresentazione virtuale che permette di avere sempre sotto controllo quella reale, riducendo i costi d’intervento e anticipando possibili guasti.
– Phoenix Contact (Bad Pyrmont e Blomberg, Germania), produttore di componenti elettriche, ricorre al “gemello digitale” con un altro obiettivo: non c’è una rappresentazione digitale delle macchine ma delle specifiche di ciascun cliente. I tempi di produzione sono stati ridotti del 30%.
– Procter & Gamble (Rakona, Repubblica Ceca) raccoglie e usa i dati per monitorare ed effettuare simulazioni sulla filiera produttiva. Il processo è diventato più efficiente e il tasso di soddisfazione dei clienti è più che raddoppiato.
– Sandvik (Gimo, Svezia) è un gruppo attivo nell’ingegneria dei materiali e nel settore minerario. Ha digitalizzato la produzione, capace adesso di adattarsi anche nei turni non presidiati dalla presenza umana.
– Saudi Aramco (Uthmaniyah, Arabia Saudita) è un impianto di trasformazione del gas. Utilizza sensori e intelligenza artificiale. Le ispezioni vengono effettuate da droni e gli addetti sono accompagnati da caschi intelligenti e altre tecnologie indossabili. I tempi delle operazioni si sono così ridotti del 90%.
– Schneider Electric (Le Vaudreuil, Francia) ha messo l’intelligenza artificiale al centro, favorendo la condivisione di informazioni e buone pratiche su manutenzione e consumo energetico. I costi legati all’energia sono diminuiti del 10%, quelli di manutenzione del 30%.
– Siemens Industrial Automation (Chengdu, Cina) ha creato una piattaforma capace di prendere gli ordini dei clienti, gestire le risorse necessarie per completarli, pianificare i tempi di produzione e consegna.
– Tata Steel (IJmuiden, Olanda) ha uno stabilimento da 9.000 dipendenti che, scrive il report, “mette le persone al primo posto. Ha creato “un’accademia” che aiuta i lavoratori a trovare soluzioni per ridurre gli sprechi e migliorare la qualità e l’affidabilità dei processi di produzione. Ne hanno beneficiato i risultati finanziari.
I 5 “comandamenti” dell’Industria 4.0
Lo studio individua alcune “evidenze”. Non si tratta di principi o sondaggi ma di riscontri che, come chiariscono i 16 impianti-faro, sono già realtà.
Europa e Asia guidano la rivoluzione – “La rivoluzione digitale è arrivata ed è in atto un cambiamento di paradigma nella produzione globale”. I fari coprono diversi settori, ma si concentrano in Europa (con 9 impianti) e Asia (6 impianti), mentre negli Stati Uniti ce n’è solo uno. È “la conferma del fatto che queste regioni sono all’avanguardia in termini di adozione tecnologica”.
Accodarsi non basta – Chi si è mosso per primo è “in anticipo di anni rispetto ai concorrenti”. Chi resta fermo è spacciato, ma anche accodarsi potrebbe non bastare. Oltre a penalizzare la propria impresa, si rischia di “mettere a repentaglio l’intero settore manifatturiero”. La soluzione è “accelerare drasticamente lo sviluppo del digitale, imparando dagli stabilimenti ‘faro’ e lavorando insieme per superare gli ostacoli all’adozione”.
Chi vince prende tutto – Rincorrere potrebbe comunque non bastare. Chi ha fatto in fretta, come i fari, sta già raccogliendo “benefici smisurati”. Tanto che si può già “scorgere una dinamica in cui ‘i vincitori prendono tutto’, simile alla prima rivoluzione internet, dove alcuni precursori hanno ottenuto i maggiori vantaggi della creazione di valore: 9 aziende su 10 hanno già accumulato un anno di ritardo e perfino i leader di settore sono bloccati in progetti pilota”.
Digitalizzare su vasta scala – Si deve andare oltre i progetti pilota, per abbracciare la digitalizzazione “su ampia scala”. È un modo per “rafforzare la resilienza e la produttività”. Agilità e produttività sono infatti strumenti per reggere “alla crisi economica e ad altri shock”. L’applicazione su scala “consente al tempo stesso i benefici in termini di crescita, costi e flessibilità”. Fa quindi bene alle casse, ma non solo: permette di “affrontare eventuali problematiche”.
La fabbrica torna attraente – “I fari sono la prova dei benefici della rivoluzione digitale in termini di produttività, agilità e personalizzazione di massa, creano nuovi modelli di business e iniettano capitale umano per rendere i luoghi di lavoro rivolti alla produzione attraenti e interessanti, dimostrando il potenziale dei sistemi di produzione avanzati per affrontare le sfide globali, guidare la nuova crescita e rendere la produzione un luogo di lavoro allettante”.
Se avete correzioni, suggerimenti o commenti scrivete a dir@agi.it.
Se invece volete rivelare informazioni su questa o altre storie, potete scriverci su Italialeaks, piattaforma progettata per contattare la nostra redazione in modo completamente anonimo.