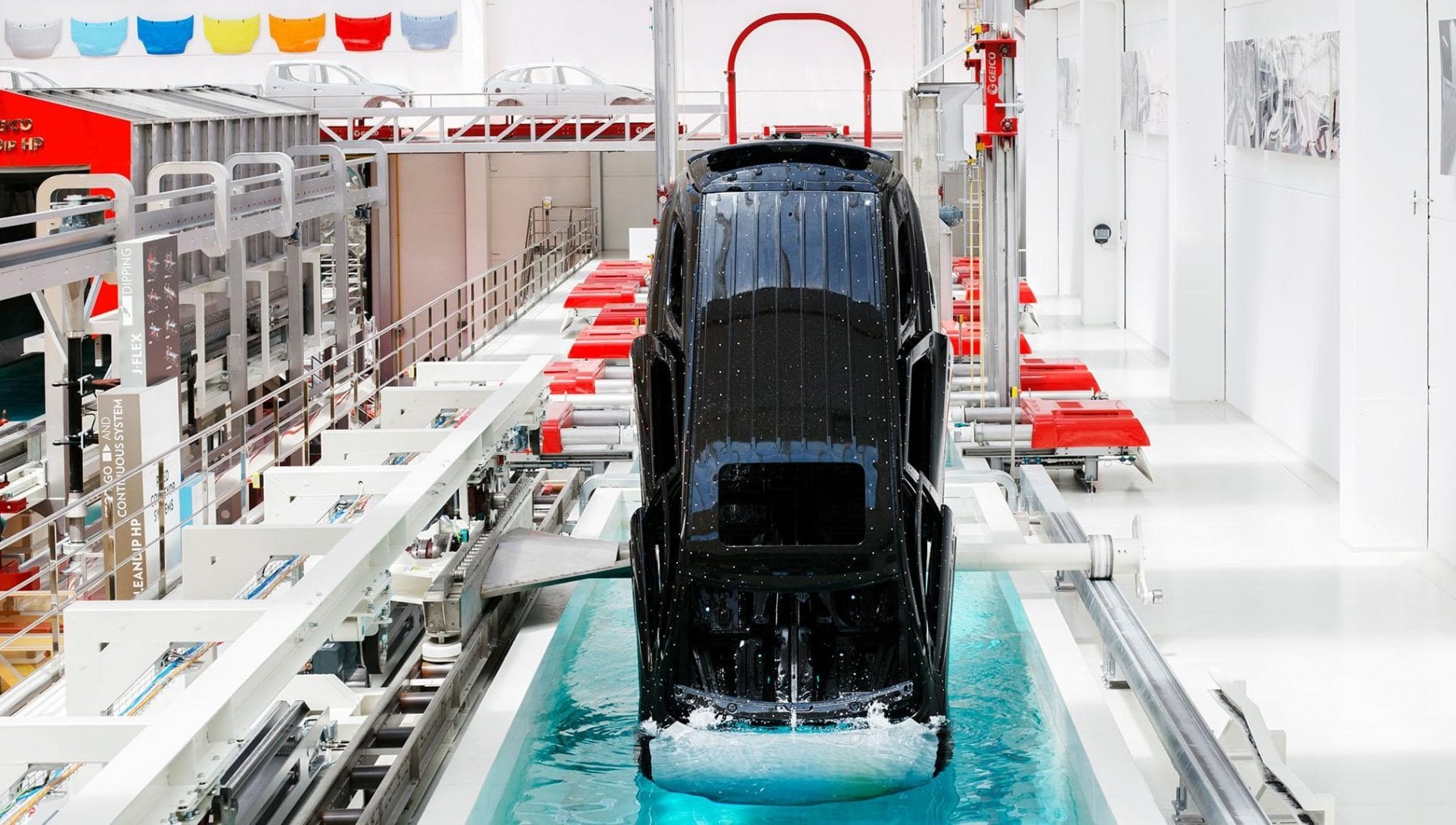
ROMA – GeicoTaikisha si è aggiudicato un’importante commessa da Psa Peugeot-Citroen. Il Gruppo italo-giapponese leader mondiale nella progettazione di impianti chiavi in mano per la verniciatura delle scocche auto, realizzarà così l’impianto di verniciatura dei veicoli prodotti nello stabilimento della casa transalpina Gliwice, in Polonia. “Gli impianti di Geico sono in grado di adattarsi ad esigenze produttive in costante cambiamento, rispondendo ai bisogni dei singoli clienti secondo una logica di mass customization – ha dichiarato il nuovo ceo della società italo-nipppnica, Daryush Arabnia – Per ottenere questi risultati, d’altra parte, è indispensabile non solo aggiornare continuamente il livello dell’innovazione tecnologica ma, nello stesso tempo, lavorare sull’approccio culturale che si ha nei confronti del progresso in quanto tale. Per questo ritengo sia giusto parlare di innovazione a 360 gradi, tenendo conto della valenza meramente tecnologica e di quella più propriamente umana. Solo su queste basi si costruisce una squadra, cioè uno staff unito e coeso, in grado di affrontare livelli di competizione sempre più stringenti”.
L’elemento vincente che ha permesso alla GeicoTaikisha di acquisire la commessa di Psa è stato la velocità di esecuzione dei lavori poiché il nuovo e moderno impianto sarà realizzato in 15 mesi (contro i circa 24 mesi dei tempi standard per la progettazione e la realizzazione dell’impianto chiavi in mano), imponendo livelli di produttività molto elevati nonostante i necessari adattamenti alla struttura preesistente. Il merito della velocità di esecuzione è frutto dello “smart design”, ovvero l’insieme di tools innovativi e di pratiche che permettono di ridurre drasticamente il periodo di consegna di un impianto di verniciatura mantenendo standard di qualità elevati. Tutto il processo di smart design viene implementato all’interno del “Pardis Innovation Centre”, la massima espressione dell’approccio innovativo di GeicoTaikisha, il più importante centro di ricerca e sviluppo a livello globale basato a Cinisello Balsamo (MI) inaugurato nel 2009 con un investimento complessivo di oltre 60 milioni di euro che ospita più di 40 prototipi funzionati, molti dei quali in ottica 4.0. Grazie al know-how acquisito, nella fase di ricerca, sviluppo e prototipazione i tecnici di GeicoTaikisha applicano modelli matematici (Cfd – Computational Fluid Dynamics) che permettono di simulare i processi fisici di termodinamica propri di un impianto di verniciatura.
Analogamente, l’ottimizzazione dei flussi delle scocche e dei materiali all’interno degli impianti viene ottenuta attraverso dinamiche di simulazione (Des – Discrete Event Simulation), mentre il Parametric Modeling, ovvero la realizzazione di parti di impianto in 3D parametriche, permette la modifica in tempo reale di tutte le componenti di ingegneria, rendendo rapida ed efficace la realizzazione. Inoltre, grazie a una stanza fisica e all’utilizzo di software di realtà immersiva (Iel – Interactive Engineering Laboratory), è possibile “navigare” nell’impianto in 3D in scala 1:1, per verificare gli ingombri e il layout in fase di progettazione, ottenendo così una drastica riduzione degli errori di progettazione. Contemporaneamente, il 4D permette la visualizzazione virtuale e la gestione delle fasi di ingegneria, montaggio e collaudo attraverso un “Gant” per verificare in tempo reale lo stato di avanzamento del progetto. Infine, la scansione laser realizza un 3D digitale degli impianti esistenti per verificare la progettazione, la realizzazione e l’installazione di nuove apparecchiature, soprattutto nel caso di una struttura già esistente. Grazie quindi all’approccio altamente innovativo, le fasi di ingegneria “standard” in GeicoTaikisha si possono implementare addirittura prima dell’arrivo della commessa, grazie a un sistema di parametralizzazione inglobato in grado di adattarsi alla specificità di ogni singolo progetto. “Detto in altri termini – ha concluso Daryush Arabnia – la standardizzazione progettuale di alcune parti avvantaggia il tempo dedicato alla customizzazione. Infatti, il cosiddetto ‘zoccolo duro’ della fasi di lavorazione viene gestito più rapidamente.
Se solo pochi anni fa per iniziare lo step della fabbricazione erano necessari almeno 6 mesi, ora poche settimane sono sufficienti. Questo permette anche di dedicare maggiore attenzione ai dettagli e alla qualità e, in parallelo, riservare più tempo allo sviluppo del business. Soprattutto a livello tecnico occorre scalfire il blocco culturale, equilibrando mentalità del “controllo” con quella di fiducia negli strumenti. In precedenza la produzione standard costituiva per l’industria un miraggio, ora, invece, cambiando l’approccio mentale si concede a questo tipo di lavorazione più spazio, sperimentandone le possibilità concrete di implementazione”. (m.r.)
Fonte www.repubblica.it