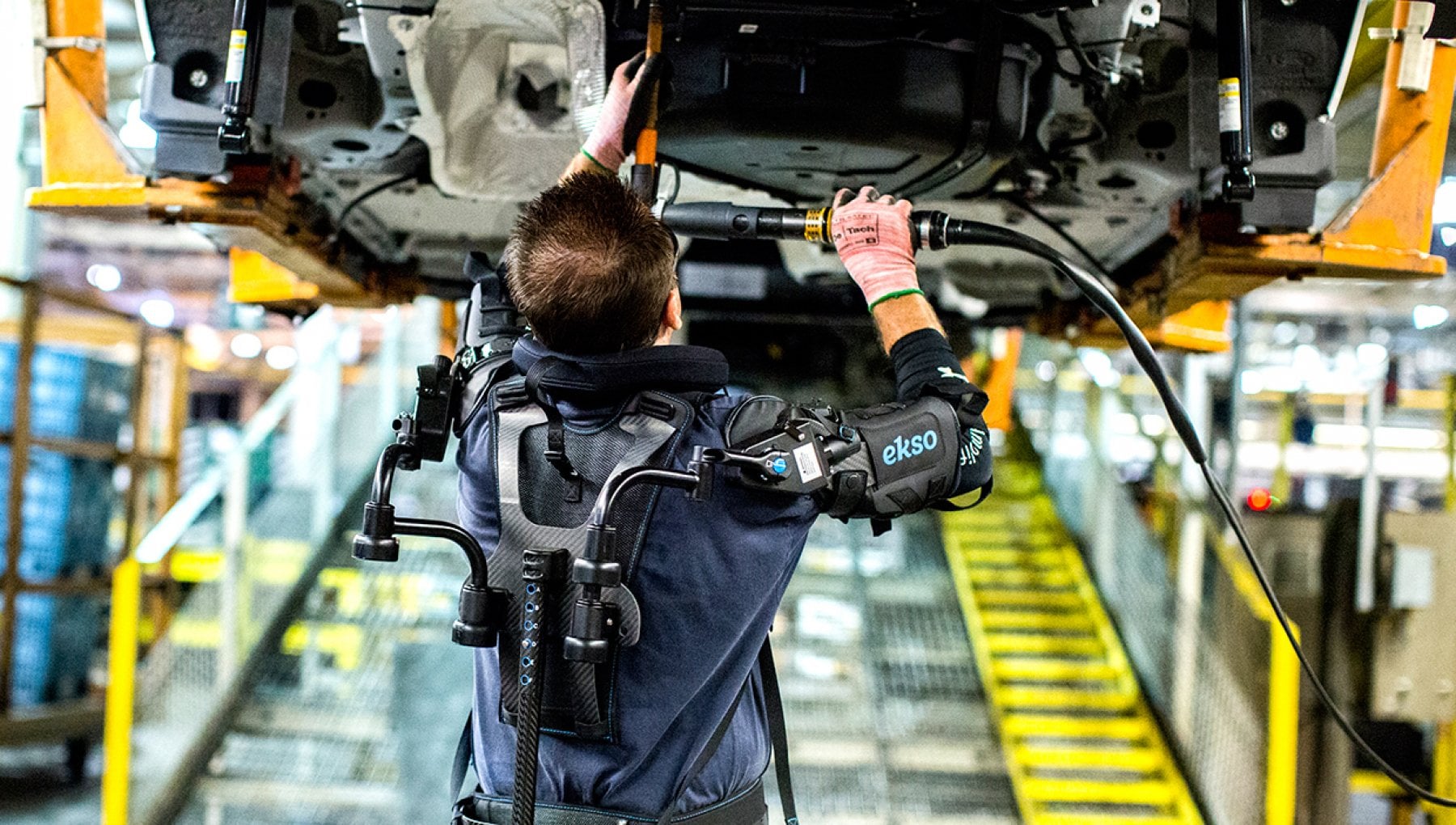
ROMA – Avete presente Tony Stark che grazie a un’armatura supertecnologica diventa Iron Man? Tra qualche anno potrebbe accadere la stessa cosa agli operai addetti alla catena di montaggio delle aziende automobilistiche. Oltre ai robot che sostituiscono il lavoro dell’uomo infatti, in fabbrica potrebbero entrare anche gli esoscheletri, ovvero dispositivi tecnologici che si applicano sul corpo per sostenere la muscolatura e la tenuta delle ossa, che aiutano i lavoratori a svolgere le attività manuali più faticose e ripetitive, evitando gli infortuni e rendendo meno frequenti le malattie professionali tipiche dei lavori usuranti. Nonostante la crescente robotizzazione del processo produttivo, infatti, ci sono operazioni, lungo le linee di assemblaggio finale, dove il lavoro umano non è sostituibile ed è opportuno utilizzare personale esperto, spesso quindi non più giovane. Insomma le fabbriche avranno sempre più bisogno di esocheletri.
Secondo ABI Research, il potenziale richiesto dal mercato sarebbe di 60 mila unità, con un tasso di crescita previsto dal 2019 al 2024 di oltre il 50%. La Hyundai in Corea del Sud sta già provando gli esoscheletri realizzati dalla sua divisione Hyundai Rotem, uno per aiutare i dipendenti a svolgere le attività sopraelevate e un altro che si trasforma in sedia per far completare ai lavoratori le attività senza piegarsi, e prevede di spedirli anche in una delle sue fabbriche in Alabama, sperando poi di venderli anche ad altre case automobilistiche.
Gm invece sta testando in Usa alcuni esoscheletri prodotti dalla ULS Robotics, un’azienda con sede a Shanghai, e anche Ford ha intenzione di farlo. In collaborazione con la Ekso Bionics, con sede in California, è nato EksoVest, un esoscheletro regolabile che può essere indossato da persone con corporatura diversa, che funziona sfruttando un sistema idraulico per redistribuire i carichi, aiutando a sollevare i pesi e riducendo lo sforzo fino a 7 chilogrammi circa. L’esoscheletro, ancora in fase sperimentale, è impiegato in due test distinti con una decina di operai in due stabilimenti di Ford a Detroit. L’azienda è però interessata a sperimentarlo anche in altri siti in giro per il mondo, in vista di un suo eventuale impiego su larga scala. Audi sta conducendo test approfonditi su due progetti diversi, il Paexo Ottobock e lo Skelex 360, e Nissan sta ultimando le fasi di collaudo di un progetto che prevede l’integrazione di un sistema di esoscheletri nelle linee di produzione dello stabilimento spagnolo di Zona Franca, a Barcellona, per poi applicarlo anche ad altri impianti.
In Italia, invece, un consorzio formato dalle aziende Comau (Piemonte) e Ossur (Emilia Romagna) ha avviato di recente una collaborazione per lo sviluppo di esoscheletri con Iuvo, nata da un pezzo dell’Istituto di Bio Robotica della Scuola Superiore Sant’Anna di Pisa. L’iniziativa è ancora in fase di avvio. Ma se gli esoscheletri rappresentano una risorsa per gestire l’invecchiamento della popolazione lavorativa, è molto importante monitorarne l’efficacia sia in termini di valutazione del carico biomeccanico (con l’obiettivo di riduzione dello sforzo muscolare e della fatica), sia di possibile impatto psico-sociale sull’essere umano. Dal 2017 proprio con un approccio integrato il Politecnico di Torino ha partecipato a una campagna di prove che ha coinvolto una trentina di operatori di Fca e una decina di suoi team leader. I soggetti volontari hanno provato alcune tipologie di esoscheletri passivi per arti superiori, tra cui l’esoscheletro Mate, progettato e sviluppato da Comau, rispetto ad attività sottoscocca che richiedono di lavorare a braccia alzate. Insomma lo sviluppo dell’ergonomia nella fabbrica è molto promettente, ma l’obiettivo deve essere quello di rendere i robot collaborativi (cobot) dei veri compagni di lavoro e non degli intrusi che dettano all’uomo tempi e ritmi senza tener conto della variabilità del comportamento umano. Ed è questo l’obiettivo dell’Industria 5.0: una fabbrica a misura del singolo lavoratore.
Fonte www.repubblica.it